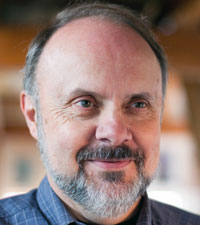
The organ workshop of Paul Fritts & Co. in Parkland WA has recently completed the delivery and installation of Opus 37 for the Basilica of the Sacred Heart on the campus of the University of Notre Dame in South Bend, IN.
The organ is the firm’s largest to date, with 69 stops and 4 manuals. There are some 5,164 pipes including a full-length 32’ Posaune in the Pedal.
The organ has numerous firsts for the company:
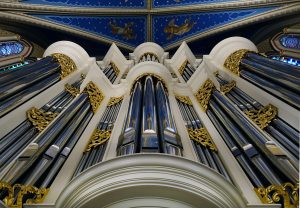
The majority of the pipework for the organ is made from tin/lead alloys that have been cast on sand instead of the previous method of casting the metal sheets on top of a cloth-covered slab of stone. The sand casting is a more ancient method of preparing the metal that causes the molten metal to cool much more quickly than on the stone slab. This rapid cooling causes the crystals which form in the metal as it solidifies to be much smaller than when the metal is allowed to cool more slowly. This crystal structure imparts a subtle but important character to the metal that seems to promote elegant pipe speech and a colorful sustained sound.
It is the first 4-manual organ built by the Fritts workshop.
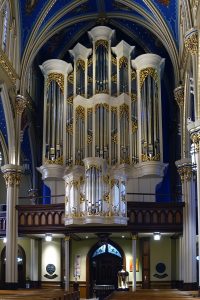
It is the first organ by the company to incorporate both German and French reed stops on the same divisions. French reeds at 16’ and 8’ pitch in the Pedal, at 8’ and 4’ pitch in the Great and a Cromorne 8’ in the Rückpositive join the Cavaille-Coll style Hautbois 8’ in the Swell to add substantially to the ability of the organ to play French literature.
There is also a Renaissance-style Trompet 8’ in the Swell which is patterned after those built by the great North German Scherer family of organ builders.
The organ makes use of “thermally-modified” lumber in the playing action (keyboards, backfall levers, couplers, etc.) as well as in the windchests for sliders and toeboards. This material is the result of a new way of treating wood that has been cured at a high temperature in kilns where the oxygen has been removed to prevent the wood from burning. The high temperatures cause the cells of the wood to seal off effectively, making the wood resistant to absorbing or giving off moisture and thus remaining very stable dimensionally. The result is that dimensionally-critical parts of the organ remain stable throughout seasonal swings in the humidity level.
The organ is also the first to use carbon fiber rods as trackers throughout the instrument. These, too, are entirely impervious to humidity changes, which is especially important in a large instrument with very long tracker runs. An added benefit is their lower mass.
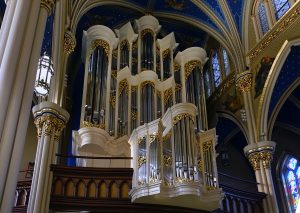
As in all of the larger Fritts organs, the Notre Dame instrument has “dual” stop action. The stop action is first and foremost mechanical with the drawknobs being physically attached to the windchest sliders. Electric solenoids can move the stops when thumb pistons or toe studs are depressed. These solenoids are controlled by a sophisticated computer system that has 999 levels of memory, meaning that all of the pistons and toe studs can be set 999 different times. Additionally, this is the first use of so-called “intelligent” solenoids that incorporate optical sensors to monitor the movement of the solenoid during the actual motion. If the solenoid is moving too slowly, the computer can send additional amperage to speed up the movement. It can also slow down a solenoid that is moving too quickly. The motion of the solenoid is also monitored to reduce the current as the slider reaches the end of its travel to quiet the system.
The organ was set up in the Basilica and voiced and tuned very quickly and efficiently. The entire process, from the unloading of the trucks to the tuning of the final pipe, required just 81 days. Preparation of the organ in the workshop along with the shop voicing of the flue pipes, and especially the careful voicing of the reed pipes on the actual windchests in the organ in the shop, contributed substantially to the savings of time during the installation.
Both the visual and sonic impacts of the organ in the Basilica have exceeded the expectations of all involved in the project. It is hoped that the organ will serve as an inspiration for both worship in the Basilica and for the organ students and other performers for many generations to come.
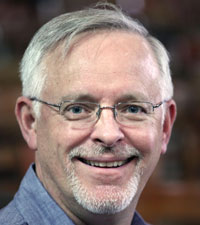
Please stop by the Basilica to see and hear the new instrument if you are in the South Bend area.
Bruce Shull
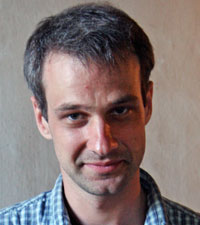
Listen to Erik McLeod improvising on some of the “bigger sounds” of the Notre Dame organ.